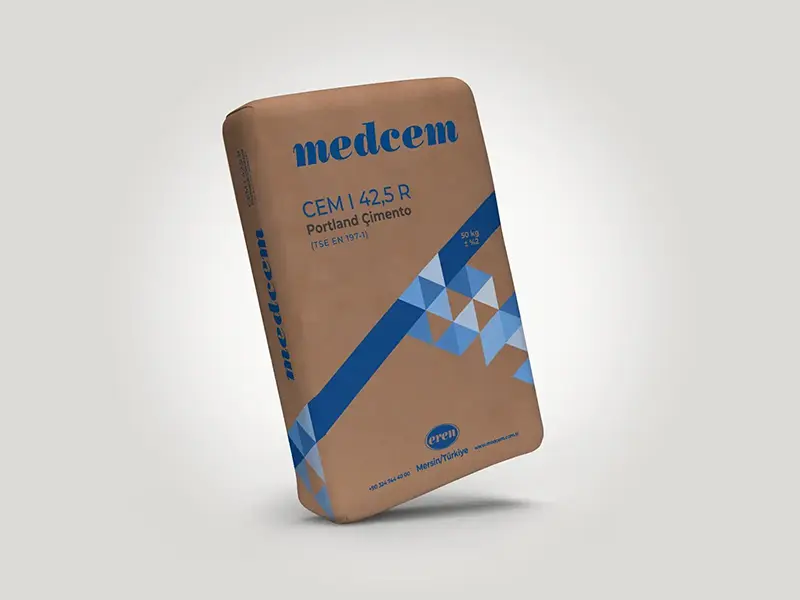
Çimento nedir?
Çimento, inşaat sektöründe yaygın olarak kullanılan bir bağlayıcı malzemedir. Ana bileşenleri arasında kalsiyum, silikon, alüminyum ve demir bulunur. Bu bileşenler, yüksek sıcaklıklarda öğütülüp karıştırılarak elde edilir ve sonrasında su ile karıştırıldığında sertleşerek betonun ana maddesi haline gelir. Çimentonun bu özelliği, yapıların dayanıklılığı ve stabilitesi için kritik öneme sahiptir.
Su ile karıştırıldığında kimyasal bir tepkimeye giren çimento, karışımın donarak sertleşmesini sağlar. Bu özellik, çimento kullanılarak yapılan yapıların dayanıklılığını arttırır. Çimento, köprülerden binalara ve barajlardan yollara kadar birçok farklı yapının inşasında temel bir malzeme olarak kullanılır. İnşaat projelerinin vazgeçilmezi olan çimento, yapıların uzun ömürlü ve güvenli olmasını sağlar.
Çimentonun Tarihçesi
Çimento, antik zamanlardan beri bilinen bir yapı malzemesidir, ancak modern çimentonun tarihçesi 19. yüzyılda İngiltere'de başlar. 1824 yılında Joseph Aspdin adında bir İngiliz mucit, Portland çimentosunu icat etti. Bu yeni çimento türü, adını İngiltere'nin Portland adasındaki benzer renkli doğal taşlardan alır.
Portland çimentosu, sıcaklık ve bileşen kontrolleri sayesinde daha önceki çimento türlerinden daha üstün özellikler sundu. Aspdin'in bu buluşu, betonun dayanıklılığını ve suya karşı direncini önemli ölçüde artırdı. 20. yüzyıl boyunca, çimento üretim teknikleri gelişti ve dünya çapında kullanımı genişledi, böylece modern inşaatın temel taşı haline geldi.
Çimento Türleri ve Özellikleri
Çimento, yapı malzemeleri arasında çok çeşitli türlerle temsil edilir ve her türün kendine özgü özellikleri vardır. Bazı yaygın çimento türleri ve bunların özellikleri şu şekildedir:
- Portland çimentosu: En genel amaçlı kullanılan çimento türüdür. İnşaatın hemen her alanında kullanılabilir, su ile karıştırıldığında hızlı bir şekilde sertleşir ve zamanla mukavemetini artırır. Portland çimentosu, beton, harç ve sıva yapımında idealdir ve mükemmel yapışma özellikleri sunar.
- Beton çimentosu: Özellikle beton üretiminde kullanılan bu çimento türü, donma ve çözülme döngülerine karşı üstün direnç gösterir. Beton çimentosu, ayrıca aşınma ve kimyasal etkilere karşı da dayanıklıdır, bu nedenle yol ve köprüler gibi dış mekan uygulamalarında yaygın olarak tercih edilir.
- Sülfat dirençli çimento: Bu çimento türü, sülfat iyonlarına karşı yüksek direnç gösterir ve bu özelliği ile sülfat bakımından zengin topraklarda veya endüstriyel atıkların olduğu alanlarda kullanım için uygundur. Sülfat dirençli çimento, altyapı projelerinde ve kanalizasyon sistemlerinde tercih edilir çünkü yapısal bütünlüğü sülfat saldırısına karşı korur.
- Alçak ısı çimentosu: Büyük beton hacimlerinin dökümü sırasında daha az ısı üretir ve bu sayede ısı nedeniyle oluşabilecek çatlakları önlemeye yardımcı olur. Alçak ısı çimentosu özellikle barajlar ve büyük ölçekli betonarme yapılar için idealdir, çünkü bu yapılar sıkıştıkça ve genleştikçe yavaş yavaş sertleşir.
- Hızlı sertleşen çimento: Acil durum onarımları veya hızlı mukavemet kazanımı gerektiren diğer uygulamalar için idealdir. Hızlı sertleşen çimento, trafik gibi hızlı yüklenme gerektiren alanlarda beton dökümü için kullanılır ve çok kısa sürede yüksek mukavemet değerlerine ulaşır.
- Beyaz çimento: Yüksek estetik değer gerektiren uygulamalar için kullanılır. Beyaz çimento, renkli beton ürünleri, mozaikler ve dekoratif sıva işleri için mükemmeldir. Ayrıca, gri çimentonun aksine, renkli pigmentlerle kolayca karıştırılabilir ve çeşitli renk seçenekleri sunar.
Bu çimento türleri, projenin gereksinimlerine uygun özellikler sağlayarak, inşaat mühendisliğinde geniş bir uygulama yelpazesi sunar. Her çimento türünün kullanımı, belirli koşullar ve ihtiyaçlar göz önünde bulundurularak belirlenmelidir.
Çimento Hammaddeleri
Çimento üretimi için gerekli olan hammaddeler, çimentonun kimyasal bileşimi ve özellikleri üzerinde doğrudan bir etkiye sahiptir. Bu hammaddeler doğal kaynaklardan sağlanır ve çimentonun mukavemetini, dayanıklılığını ve diğer özelliklerini belirler.
- Kalker (kalsiyum karbonat): Çimento üretiminin temel bileşenidir. Kalker, çimentonun ana maddesi olan kalsiyum oksit sağlar. Yüksek sıcaklıklarda kalker, kalsiyum oksite dönüşür ve çimentonun temel yapı taşını oluşturur.
- Kil: Kil, alüminyum ve silisyum oksitleri açısından zengindir ve çimentonun kimyasal yapısını dengelemek için kullanılır. Kil, çimentonun sertleşme sürecinde ve sonrasında gerekli olan yapışma özelliklerini ve mukavemetini sağlar.
- Demir oksit: Çimentonun rengini ve sertleşme özelliklerini etkileyen bir başka önemli madde demir oksittir. Ayrıca, çimentonun termal özelliklerine katkıda bulunur ve yapısal bütünlüğü artırır.
- Alüminyum oksit: Genellikle kil içinde doğal olarak bulunan alüminyum oksit, çimentonun erken mukavemet kazanımını hızlandırır ve sertleşme sürecini iyileştirir. Bu madde, çimentonun kimyasal reaksiyon hızını artırarak daha hızlı sertleşmesine yardımcı olur.
- Diğer katkı maddeleri: Kireçtaşı gibi katkı maddeleri de çimento karışımına eklenir. Kireçtaşı, çimentonun donma süresini ayarlamak için kullanılır ve aşırı erken sertleşmeyi önleyerek işlenebilirliği artırır. Ayrıca, çimentonun dayanıklılığını ve nihai kullanım özelliklerini iyileştirmek için çeşitli kimyasal katkılar eklenir.
Bu hammaddeler, uygun oranlarda karıştırılarak yüksek sıcaklıklarda işlenir ve sonuç olarak dayanıklı, mukavemetli bir bağlayıcı malzeme olan çimento elde edilir. Çimento, modern inşaatın vazgeçilmez bir parçası olarak, yapıların uzun ömürlü ve güvenli olmasını sağlar.
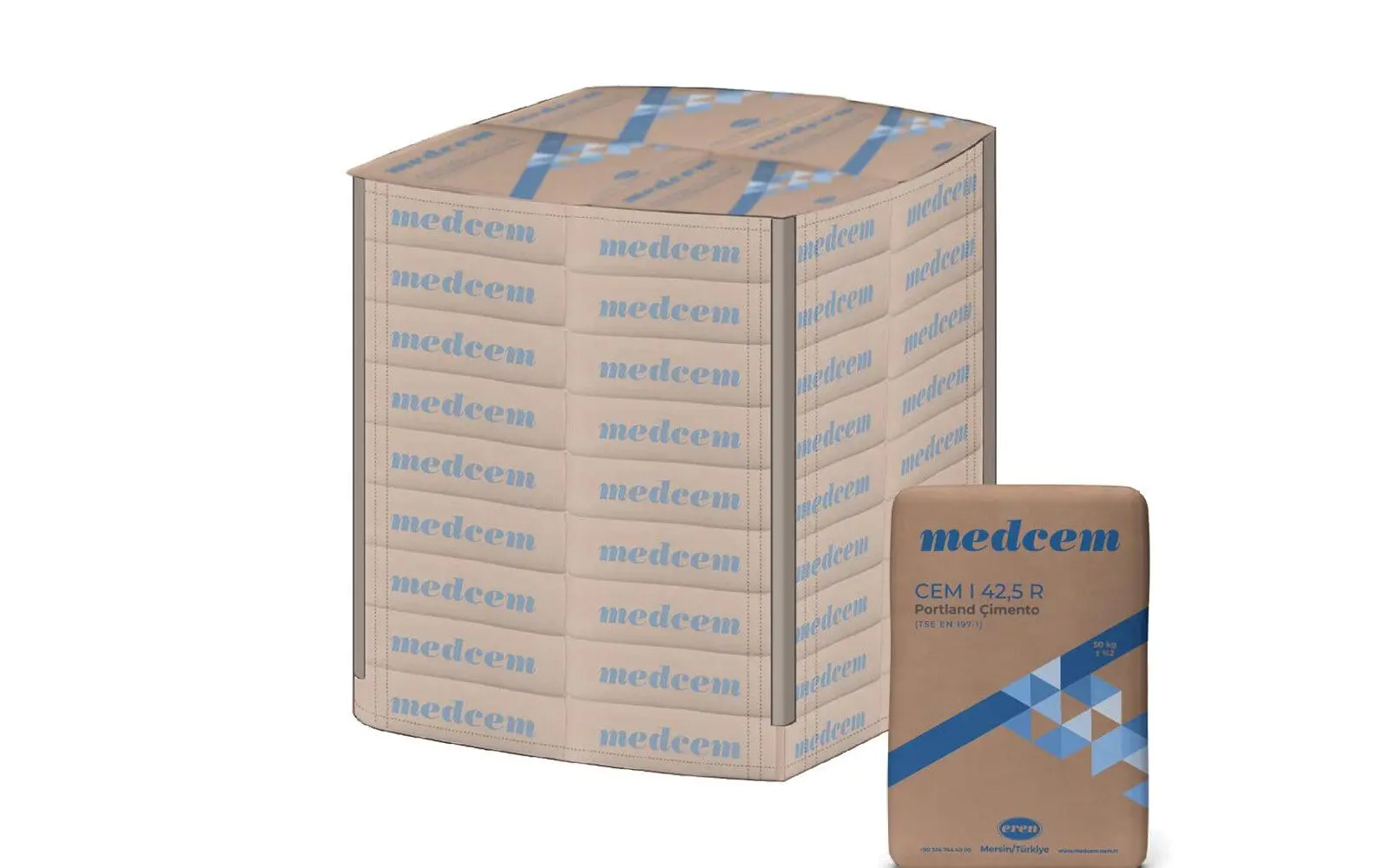
Çimento Üretim Süreci
Çimento üretimi, karmaşık bir süreçtir ve genellikle aşağıdaki adımları içerir:
- Hammaddelerin hazırlanması: Kireçtaşı ve kil, maden ocaklarından çıkarılır ve önce kırma ve öğütme işlemlerinden geçirilerek toz haline getirilir. Bu adımda, diğer katkı maddeleri de karışıma eklenir.
- Karıştırma ve homojenizasyon: Kireçtaşı, kil ve diğer katkı maddeleri doğru oranlarda karıştırılarak homojen bir karışım elde edilir. Bu aşamada, ham karışıma bazen ek hammadde ve yan ürünler de eklenir
- Klinker oluşumu: Hazırlanan ham karışım, yüksek sıcaklıkta (1400-1500°C) bir fırında pişirilir. Bu süreçte, hammaddeler kimyasal reaksiyonlara girerek klinker adı verilen türe dönüşür. Klinker, çimento üretiminin temel bileşenidir ve hidrasyon süreciyle çimento oluşumunu sağlar.
- Klinkerin öğütülmesi: Pişirme işleminden sonra klinker, öğütme işlemine tabi tutularak toz haline getirilir. Bu öğütme işlemi, çimento partiküllerinin boyutunu kontrol eder ve çimento özelliklerini belirleyen yüzey alanını artırır.
- Çimento katkı maddeleri: Öğütülen klinkere, çeşitli katkı maddeleri eklenir. Bu katkı maddeleri çimento özelliklerini iyileştirmek, çalışma süresini kontrol etmek, dayanıklılığı maksimum düzeyde artırmak veya çevresel etkileri azaltmak için kullanılır. Örnek olarak, uçucu kül, yüksek fırın cürufu, cüruf gibi katkı maddeleri verilebilir.
Çimento Uygulamaları
Çimento, inşaat sektöründe çok yönlü ve önemli bir rol oynar, özellikle hazır beton üretimi için temel bir bileşen olarak öne çıkar. Beton, çimento, su ve agrega gibi malzemelerin karışımından oluşur ve yapıların ana yapı taşıdır. Ayrıca, çimento temelli harç kullanılarak tuğla, blok, sıva ve fayans gibi çeşitli yapı malzemeleri üretilmektedir.
Çimento, prefabrik parçalar, borular ve zemin kaplamaları gibi yapı malzemelerinin üretiminde de temel bir bileşendir. Bu çeşitlilik, çimentonun inşaat endüstrisindeki kritik önemini göstermektedir. Dayanıklılığı ve uzun ömürlülüğü sayesinde, çimento inşaat projelerinde vazgeçilmez bir malzeme haline gelmiştir.
Çimentonun Kullanım Alanları
Çimentonun kullanım alanlarından bazıları şunlardır:
- Deniz yapıları ve liman inşaatları: Çimento, deniz suyu ve sert hava koşullarına dayanıklı beton üretiminde kullanılarak dalgakıran, iskele, rıhtım ve liman yapılarında uzun ömür ve sağlamlık sağlar.
- Yeraltı inşaatları ve tüneller: Tünel inşaatlarında, çimento esaslı enjeksiyon harçları, zemin iyileştirmesi ve su yalıtımı amaçlı kullanılır. Bu sayede tünel kaplamalarının daha güvenli, sızdırmaz ve dayanıklı olması mümkün olur.
- Sanayi ve depolama alanları: Fabrika zeminleri, lojistik merkezleri ve depolar için yüksek dayanımlı beton zemin kaplamalarında çimentonun rolü büyüktür. Bu kaplamalar yüksek basınç, aşınma ve kimyasal etkilere karşı uzun süre dayanır.
- Jeoteknik uygulamalar ve zemin stabilizasyonu: Yumuşak veya gevşek zeminlerin sağlamlaştırılması için çimento enjeksiyonları ve çimento-stabilize harçlar kullanılır. Bu sayede zemin taşıma kapasitesi artarken, inşaat yapılacak alan daha güvenli hale gelir.
- Onarım ve restorasyon çalışmaları: Tarihi yapıların restorasyonunda, çatlak enjeksiyonu veya yüzey güçlendirme için çimento bazlı malzemeler tercih edilir. Çimentonun kontrollü sertleşme özelliği, eski yapıların özgün dokusunu koruyarak yapısal sağlamlık kazandırır.
- Yangın dayanımı ve özel kaplamalar: Bazı betonarme yapıların yüzeyleri, çimento esaslı özel kaplamalarla güçlendirilerek yangına ve yüksek sıcaklığa karşı direnç artırılabilir. Bu uygulama endüstriyel binalarda güvenliği destekler.
- 3D beton baskı teknolojileri: Yenilikçi inşaat yöntemlerinde, çimento esaslı karışımlar 3D beton yazıcılarında kullanılmaktadır. Bu yöntemle karmaşık geometrik formlar, hızlı ve ekonomik bir şekilde üretilebilir, yapı sektöründe tasarım esnekliği sağlanır.
Çimento Endüstrisi ve Çevresel Etkileri
Çimento üretimi, enerji yoğun bir endüstridir ve çevresel etkileri vardır. Üretim süreci, karbon emisyonlarına ve enerji tüketimine neden olur. Ayrıca, çimento fabrikalarının hava kirliliğine ve toz oluşumuna katkı da bulunması da muhtemeldir. Su kirliliği de çimento üretiminin bir yan etkisi olabilir, çünkü üretim süreci su tüketimini gerektirir.
Ancak çimento endüstrisi, çevresel etkileri azaltmak için sürdürülebilirlik çabalarına odaklanmaktadır. Enerji verimliliği, alternatif yakıtların kullanımı, atık yönetimi ve karbon azaltımı gibi konular çimento endüstrisi için önemli gündem maddeleridir.
Çimento Üretiminde Kalite Yönetimi
Çimento üretiminde kalite yönetimi büyük bir öneme sahiptir. Standartlar ve belgelendirme süreçleri, çimento üreticilerinin kalite standartlarını karşılamasını sağlar. Numune alma ve deneyler, çimento kalitesinin kontrol edilmesinde kullanılan yöntemlerdir.
Fiziksel ve kimyasal analizler, çimento özelliklerinin belirlenmesine yardımcı olur. Dayanıklılık testleri, çimentonun yapısal performansını değerlendirmek için gerçekleştirilen testlerdir. Kalite yönetimi, çimento üreticilerinin güvenilir ve kaliteli ürünler sunmasını sağlar.
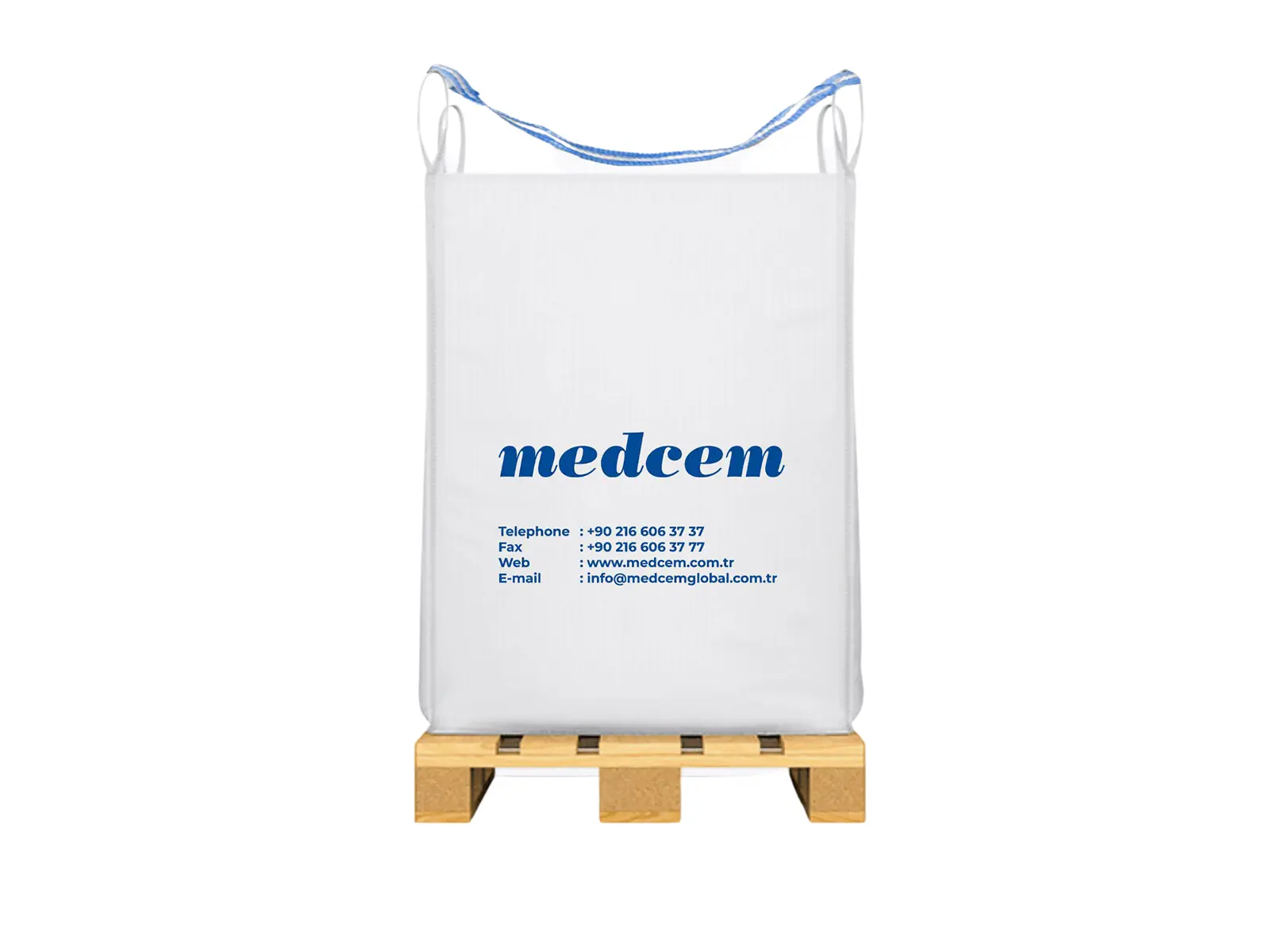
Çimento Sektörü ve Piyasa Durumu
Dünya çimento üretimi ve tüketimi sürekli olarak artmaktadır. Medcem gibi büyük çimento firmaları ve şirketler, küresel pazarda etkili rol oynamaktadır. Çimento talebi, inşaat sektöründeki büyüme, altyapı projeleri ve nüfus artışı gibi faktörlerden etkilenir.
Fiyatlar ve rekabet, çimento sektörünü etkileyen diğer önemli faktörlerdir. Yeni pazarlar ve teknolojik gelişmeler, çimento sektöründe fırsatlar yaratmaktadır. Bu faktörler, çimento üreticilerinin stratejik planlamalarında ve yatırım kararlarında belirleyici olmaktadır.
Gelecekte Çimento Teknolojileri
Gelecekte çimento sektöründe çeşitli teknolojik gelişmeler ve yenilikler beklenmektedir. Yeşil çimento üretimi, karbon azaltımı ve çevresel sürdürülebilirlik çabaları öncelikli hale gelecektir. Alternatif yakıtların ve enerji verimliliğinin kullanımı çimento üretiminde yaygınlaşacaktır.
Yeni malzemeler ve inovasyonlar, çimento özelliklerini geliştirmek ve daha sürdürülebilir yapı malzemeleri üretmek için keşfedilecektir. Ayrıca, dijitalleşme ve otomasyon da çimento üretiminde daha verimli ve güvenli süreçlere olanak sağlayacaktır.
Gelecekteki çimento teknolojileri, çimento endüstrisinin daha sürdürülebilir, verimli ve çevre dostu olmasını hedeflemektedir. Bu teknolojik ilerlemeler, inşaat sektörünün ihtiyaçlarını karşılamaya ve gelecekteki yapıların daha dayanıklı ve sürdürülebilir olmasına yardımcı olacaktır.
Çimento Sanayinde Kullanılan Kimyasal Modüller
Çimento sanayiinde kullanılan kimyasal modüller, çimentonun dayanıklılığını ve işlenebilirliğini artırmak için önemli rol oynar. Bu modüller genellikle klinker içeriğini değiştirmek, hidrasyon sürecini hızlandırmak veya yavaşlatmak ve çimento karışımının kimyasal reaksiyonlarını optimize etmek için eklenir. Yaygın kullanılan modüller arasında kalsiyum sülfat, uçucu kül ve silis dumanı bulunur.
Bu kimyasal modüller, çimentonun çevresel etkilerini azaltmak ve yapısal özelliklerini iyileştirmek için de kullanılır. Özellikle uçucu kül ve silis dumanı, atık malzemelerin yeniden kullanımı sayesinde sürdürülebilirlik sağlar. Böylece, çimento üretimi sürecinin hem performansı artırılır hem de çevre dostu bir yaklaşım benimsenir.
Türkiye'de Çimento Standartları
Türkiye'de çimento üretimi ve kullanımı, Türk Standartları Enstitüsü (TSE) tarafından belirlenen standartlara ve yönetmeliklere tabidir. TSE, çimento sektöründe kalite ve güvenliği sağlamak için belirli standartlar ve kriterler geliştirmiştir. Bu standartlar, çimento ürünlerinin performansını, dayanıklılığını ve çevresel etkilerini düzenler. Ayrıca, çimento üretimi sırasında kullanılan hammaddeler, üretim metodları ve son ürün testleri gibi konuları da kapsar.
Çimentonun belirli standartlarda üretilmesi, yapıların sağlamlığı ve dayanıklılığı açısından kritik öneme sahiptir. Bu nedenle, çimento ürünlerinin, belirlenen fiziksel ve kimyasal özelliklere sahip olması gerekmektedir. Türkiye'deki çimento standartları ayrıca, ürünlerin uygun şekilde etiketlenmesi ve pazarlanması ile ilgili hususları da içerir. Bu standartlar, tüketicilerin bilinçli seçim yapabilmesini sağlar ve sektördeki rekabet koşullarını düzenler.